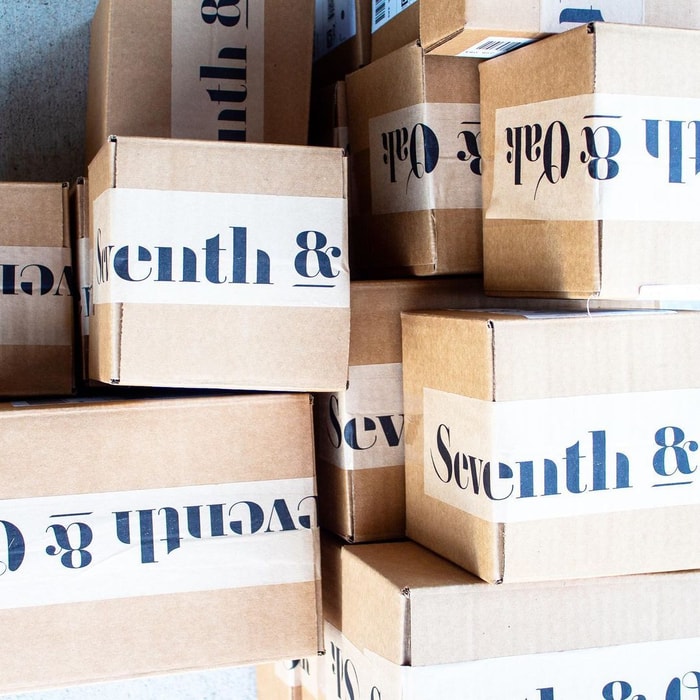
What Is Fulfillment Batching and How Does It Help Businesses?
Learn about the batch picking method and speed things up for your business! Here's how fulfillment batching works and its benefits.
By Francesca Nicasio — 06 April, 2022
Custom noissue Paper Packaging Tape by @seventhandoak
Picking remains one of the most important aspects of warehouse operations. With parcel shipping volumes likely to exceed 262 billion by 2026, the need for faster and more efficient picking processes has never been greater.
Businesses may choose from a variety of picking strategies such as batch, order, zone, wave, or cluster picking. However, your selection needs to be able to meet the unique needs of your business while speeding up the picking process significantly.
In this article, we’ll explore the batch picking method (also known as fulfillment batching) which is a popular choice among warehouse managers in many distribution centers. We’ll discuss how it works, its benefits, and how it compares with other picking methods.
What is fulfillment batching?
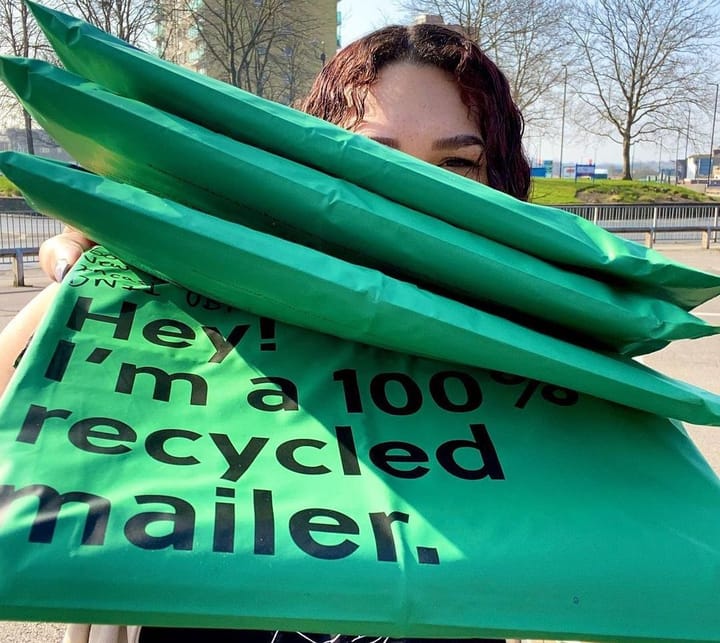
Fulfillment batching is an order picking method that allows your pickers to collect inventory for multiple orders at the same time.
In this method, multiple orders (having common SKUs) are grouped together. At a time, a picker collects multiple products of the same type, in batches. The products in each batch are then allocated to individual orders.
This ensures that warehouse employees don’t have to make repeated trips to a particular storage location, thus increasing operational efficiency. Compared to other picking methods, fulfillment batching reduces the required foot travel time since your employees need to move less around the warehouse, which speeds up the picking process.
Here’s an example to help you understand the fulfillment batching process better. Imagine that your warehouse staff has three customer orders that need to be fulfilled.
Customer A: 5 wooden spoons, 2 chef’s knives, and 1 cutting board
Customer B: 2 wooden spoons and 3 whisks
Customer C: 3 wooden spoons and 4 chef’s knives.
Instead of picking each customer’s order individually, a picker using batch picking will collect all 10 wooden spoons at the same time and put them in a designated tote on a pushcart. Next, they will collect all 6 chef’s knives and put them in another tote on the same cart.
Then they will collect the 3 whisks in another tote and finally pick the cutting board before bringing the pushcart to the sorting area. Here the items will be sorted into individual orders and packed for shipping.
Batch picking works best for businesses that process identical orders regularly. Kitting items that your customers often order together will make the fulfillment process simpler. Batch picking also works well for subscription boxes or newly launched products since most customers will get the same set of products.
What are the benefits of batch picking?
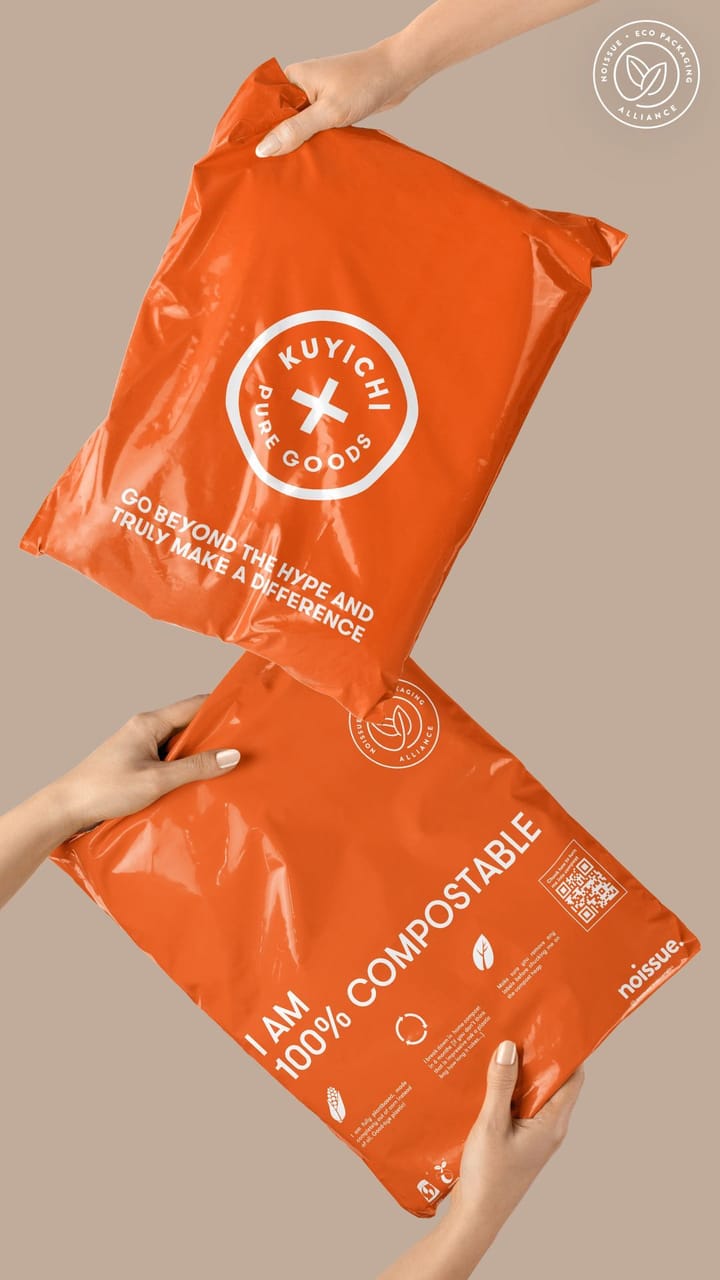
Fulfillment batching brings efficiency and speed to the order fulfillment process. It provides many advantages over other picking processes including:
1. Multiple order picking
While there are other picking methods that let you work on multiple orders at a time, none are as efficient as fulfillment batching. It’s superior because the picker needs to only collect identical items in each trip and it's easier for the packer to sort items into individual orders.
2. Less foot travel
Order fulfillment centers can be quite spacious, so making your staff collect items from multiple dispersed locations can take a significant amount of time. In batch picking, the items are homogeneous, which ensures that your pickers need to move less around the warehouse, significantly reducing the amount of time it takes to fulfill an order.
3. Faster picking rates
Speed is crucial to the success of your order fulfillment process. As such, batch picking reduces the overall time it takes to fulfill an order. It also requires less training compared to other picking methods that require your staff to memorize entire layouts of your fulfillment centers.
How batch picking works
The ecommerce fulfillment process starts when a customer places an order at your online store and it is electronically transmitted to your warehouses. Prior to this, inventory is shipped to your warehouses or distribution centers where similar items are stored together on shelves.
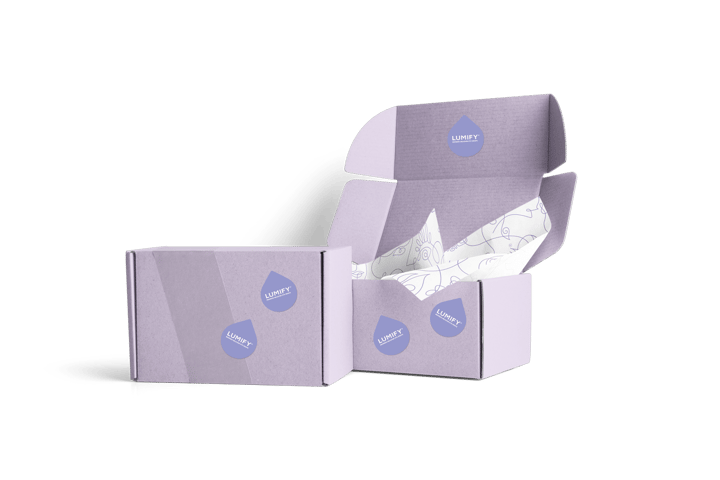
Here’s how fulfillment batching works:
Step 1: Generation of picking lists
A picking list can be generated manually or using an order management system (OMS). It’s a document that informs your warehouse staff about the items that need to be shipped to each customer.
Printed picking lists are quite rare these days as modern warehouses often use wearable devices and voice technology to assign tasks digitally.
Step 2: Grouping of orders
This stage involves the grouping of similar items from multiple orders into a single picking batch. An inventory management system or a warehouse management system (WMS) can automatically sort through orders and group batchable items together.
Step 3: Assigning batches to pickers
Next, your pickers will receive their batch picking lists. You can use your WMS to generate a batch picking list for each picker and calculate the best route so that your staff can quickly collect all the stock-keeping units needed to fulfill orders.
Step 4: Picking of items
Your staff will follow the designated routes to collect the items in their picking lists and place them in designated totes on their pushcarts. Each picker must diligently follow the designated route to eliminate time-wasting.
Step 5: Sorting and packing orders
Once the items are picked, they will be handed off to a packer. The packer is responsible for sorting items into individual orders and packing them into boxes. It is recommended that you use standard-sized boxes for different categories of products to speed up the process.
If you’re looking for custom eco-friendly shipping boxes for your brand, look no further than noissue. Our customizable Recycled Kraft boxes are perfect for shipping with most carriers including FedEx, UPS, and more.
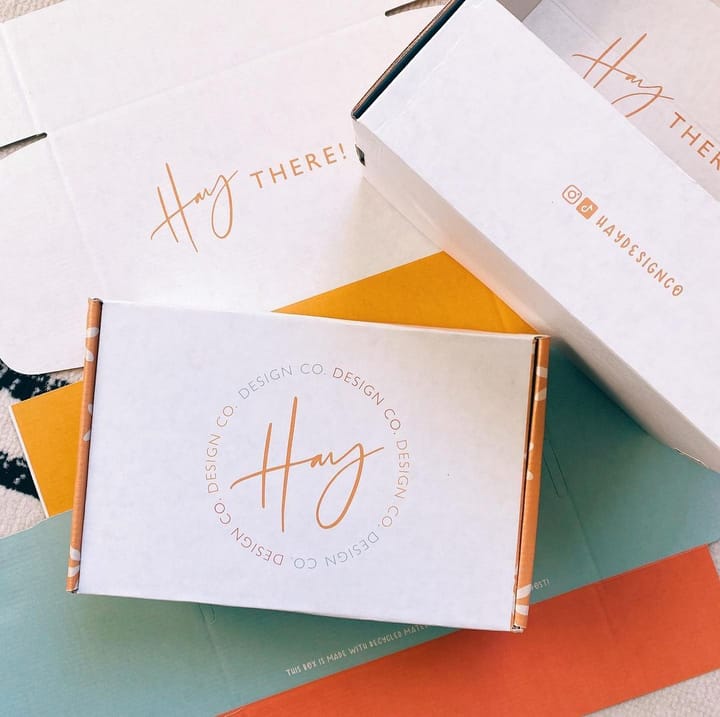
Step 6: Shipping orders
Your packer must also ensure that these boxes are securely taped and labeled so that they are ready for shipping. noissue’s Custom Tapes and Stickers offer a sustainable way to showcase your brand as well as to secure your packages. These boxes can then be placed on the loading dock for your carriers to pick them up and ship them to your customers.
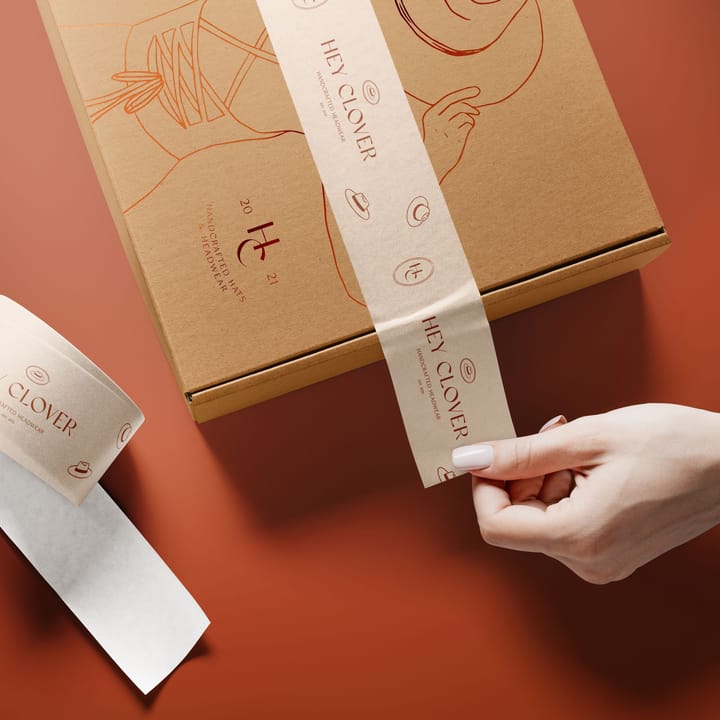
Batch picking vs single order picking
Single order picking is one of the most common picking methods that comes with its own pros and cons. It simply means that the picker will collect items for one order at a time.
It’s simpler than batch picking, but it isn’t efficient since your staff needs to retrieve items one by one. That’s why single order picking is only suitable for small businesses with low order volumes or very few SKUs to sell (so the entire inventory fits in a small room).
Batch picking vs zone picking
Zone and batch picking are considerably more efficient than single order picking. However, zone picking is completely different from batch picking.
In zone picking, a warehouse is divided into zones with designated staff assigned to each zone. Multiple pickers will collect the different items in a customer’s order from their respective zones and bring them to the packing area to be collated.
Compared to batch picking, zone picking does not require orders to be identical. It is just as efficient as batch picking, but evenly distributing the workload can be quite difficult to accomplish.
Applying automation to batch picking
A manual picking operation that involves pushing a cart throughout the warehouse to collect items takes time and increases the chances of mistakes.
An automated batch picking operation can help boost efficiency and eliminate errors. It usually requires a minimum of two automated storage devices and a batch station located in front of the access openings.
Here is how it works:
- The operator sets up the batch station with an assigned “put” location for each order.
- The operator scans the order tote and batch station location with a barcode scanner to ensure that the software knows the location of each order.
- Each order location is fitted with a “put” light to guide the operator on where to put the items.
- To select the items, the operator will initiate the automated storage units to retrieve the items in a batch
- A “pick” light on the storage device will direct the operator to pick the specified quantity of an item.
- The operator will then turn to the batch station to distribute the first items among the waiting orders using the “put” lights as a guide.
- The operator will turn back to the automated storage units to pick the next item needed for the orders.
- This process will be repeated until the current batch of orders is filled.
Wrapping it up
Batch picking offers many advantages for eCommerce businesses including greater productivity and efficiency. You can easily adopt batch picking in your warehouse operations if you often process identical orders. By automating this picking method and combining it with your OMS or WMS, you can further optimize your fulfillment process and serve your customers more quickly and efficiently.
Businesses of all sizes can become more sustainable through conscious packaging made from better materials! If you're looking for custom, creative packaging in wholesale quantities, tap our noissue Plus team here. Build your brand and design beautiful eCommerce mailers, shipping boxes, tissue wrapping paper, and more with noissue!